PCX extruders
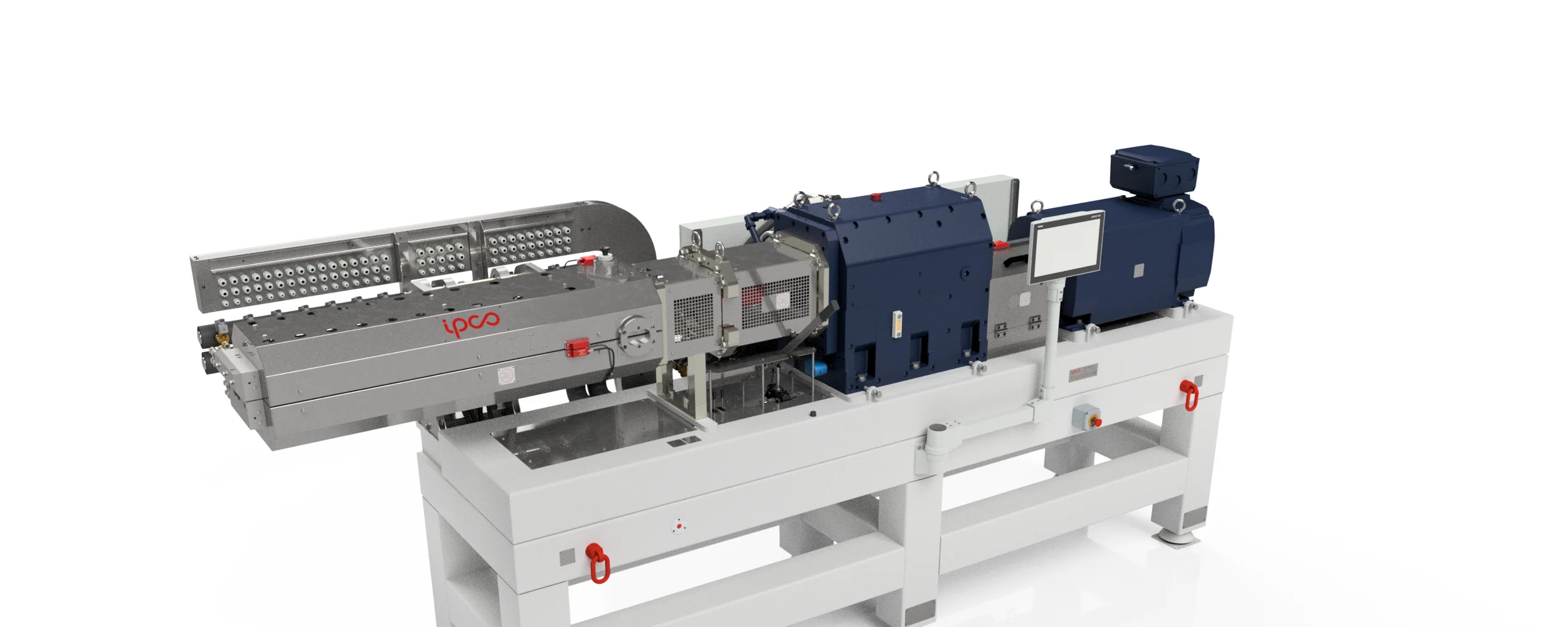
PCX extruders
IPCO’s PCX range of extruders delivers industry-leading performance and versatility for processing dry materials for thermoset powder coatings. Whether for lab-scale, small batch or high-capacity production, our extruders provide reliable, high-quality, consistent results on extruded materials due to their high torque and cooling capacity.
IPCO’s PCX range of extruders delivers industry-leading performance and versatility for processing dry materials for thermoset powder coatings. Whether for lab-scale, small batch or high-capacity production, our extruders provide reliable, high-quality, consistent results on extruded materials due to their high torque and cooling capacity.
High-performance homogenisation
IPCO’s PCX co-rotating twin-screw extruders combine precision, reliability and efficiency to ensure even dispersal and distribution of dry premix materials into a consistent and homogeneous melt.
Users benefit from productivity-enhancing features that make the system versatile enough to process all types of powder coating formulations, delivering a wide range of finishes in a single pass.
Designed for efficiency, this range handles even the most challenging materials with ease, ensuring fast return on investment.
IPCO’s PCX co-rotating twin-screw extruders combine precision, reliability and efficiency to ensure even dispersal and distribution of dry premix materials into a consistent and homogeneous melt.
Users benefit from productivity-enhancing features that make the system versatile enough to process all types of powder coating formulations, delivering a wide range of finishes in a single pass.
Designed for efficiency, this range handles even the most challenging materials with ease, ensuring fast return on investment.
High capacity
Up to 2,500 kg/h
Optimized for large-scale powder coating production
High-speed processing
Up to 1,200 rpm
Ensures efficient, consistent material homogenization
Advanced cooling
360° temperature management
Precise control for superior product quality
PCX extruders
How it works
Our PCX extruders ensure precise homogenization of dry materials, efficiently processing complex premix formulations.
The system moves materials through specialized kneading elements, where they are crushed, smeared, and shuffled with precise energy input to create a uniform melt. By effectively controlling torque-induced temperature spikes, the PCX maintains material integrity, ensuring a consistent, high-quality mix that is fresh and ready for use.
Thermoset material extrusion relies on precise temperature control within the right exposure time. The PCX excels in this, effortlessly maintaining optimal conditions, making it a class above the rest.
Material handling – The cooled feeding throats prevent bottlenecks, ensuring seamless feeding from any source – top, side, dosing or injection. This enables a high consumption rate and efficient displacement of air, allowing even low-density fine materials to be fed at comparatively high volumes.
Extrusion process – The PCX features one of the most powerful drive systems in the industry. With high-performance shafts derived from aerospace technology, it delivers uncompromised torque. Even when core-cooled for enhanced stability, these shafts remain unimpeded by the supplied power. Additionally, the extruder’s co-rotating twin screws operate at adjustable speeds of 900 or 1200 RPM, ensuring optimal homogenization across various throughput requirements.
Temperature control – With an advanced 360° ringfenced cooling system (typically across seven zones), the PCX provides unmatched material temperature management. This allows users to push throughputs beyond what competitors can achieve, without compromising product quality.
User-friendliness – Designed with safety and accessibility in mind, the PCX makes maintenance effortless. Key features include a hydraulically assisted clamshell process barrel, spring-mounted tie-down bolts, and a non-stick discharge knife. Seamless screw elements fit together in only one configuration, shafts can be changed in minutes, and interchangeable liners simplify upkeep.
Class-leading torque delivery – Each PCX extruder is mechanically scalable to the next in the range, ensuring consistent specific torque transfer to the processing material. Every component is meticulously selected for best-in-class efficiency and proven reliability.
Our PCX extruders ensure precise homogenization of dry materials, efficiently processing complex premix formulations.
The system moves materials through specialized kneading elements, where they are crushed, smeared, and shuffled with precise energy input to create a uniform melt. By effectively controlling torque-induced temperature spikes, the PCX maintains material integrity, ensuring a consistent, high-quality mix that is fresh and ready for use.
Thermoset material extrusion relies on precise temperature control within the right exposure time. The PCX excels in this, effortlessly maintaining optimal conditions, making it a class above the rest.
Material handling – The cooled feeding throats prevent bottlenecks, ensuring seamless feeding from any source – top, side, dosing or injection. This enables a high consumption rate and efficient displacement of air, allowing even low-density fine materials to be fed at comparatively high volumes.
Extrusion process – The PCX features one of the most powerful drive systems in the industry. With high-performance shafts derived from aerospace technology, it delivers uncompromised torque. Even when core-cooled for enhanced stability, these shafts remain unimpeded by the supplied power. Additionally, the extruder’s co-rotating twin screws operate at adjustable speeds of 900 or 1200 RPM, ensuring optimal homogenization across various throughput requirements.
Temperature control – With an advanced 360° ringfenced cooling system (typically across seven zones), the PCX provides unmatched material temperature management. This allows users to push throughputs beyond what competitors can achieve, without compromising product quality.
User-friendliness – Designed with safety and accessibility in mind, the PCX makes maintenance effortless. Key features include a hydraulically assisted clamshell process barrel, spring-mounted tie-down bolts, and a non-stick discharge knife. Seamless screw elements fit together in only one configuration, shafts can be changed in minutes, and interchangeable liners simplify upkeep.
Class-leading torque delivery – Each PCX extruder is mechanically scalable to the next in the range, ensuring consistent specific torque transfer to the processing material. Every component is meticulously selected for best-in-class efficiency and proven reliability.
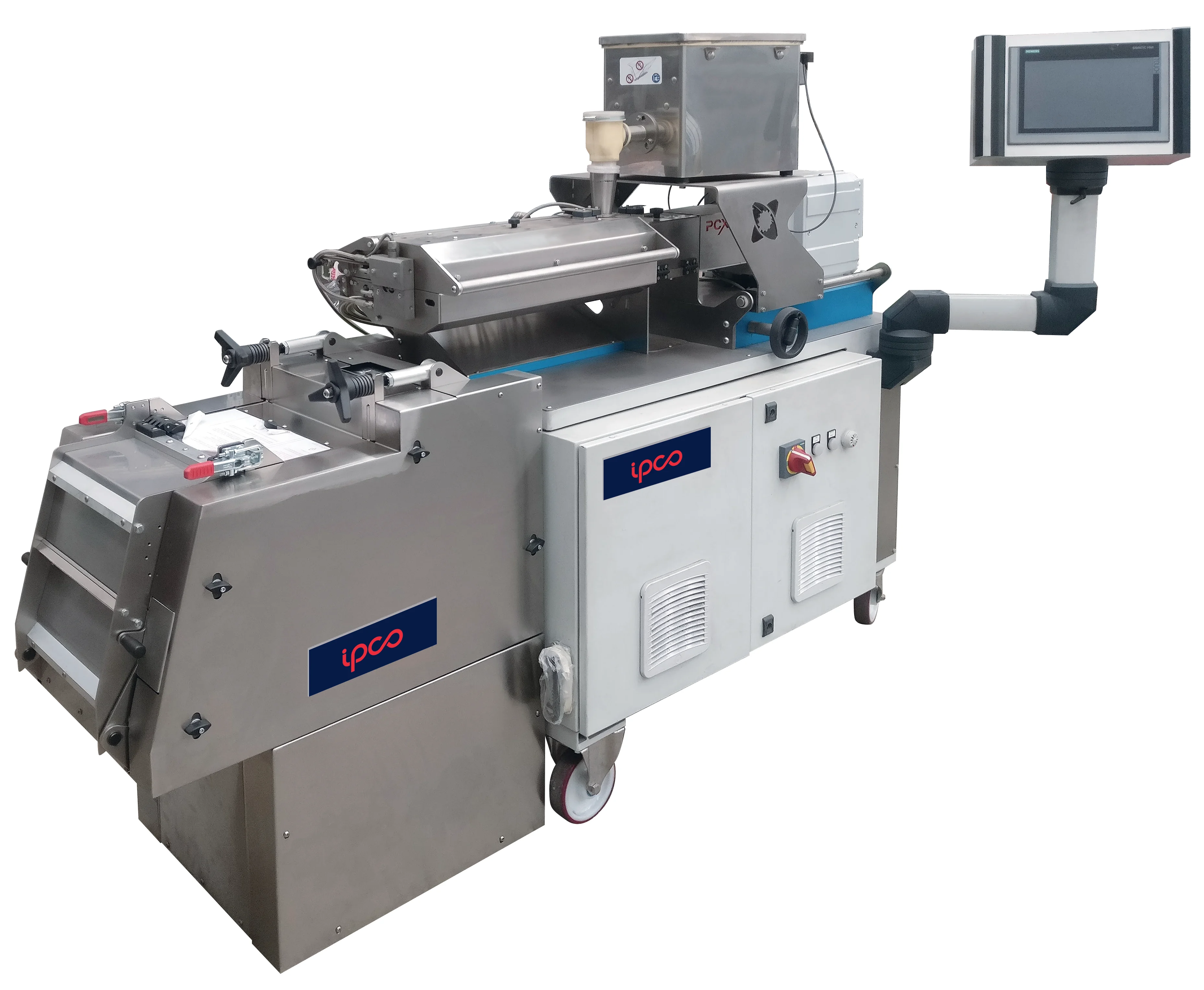
Why choose IPCO extruders?
Class-above performance – allowing for next level throughputs while maintaining standard level pricing.
Variety of finishes – textured, wrinkled, gloss, matt, metallic and more
Single-pass processing – of even the most challenging products
Easy-to-open, leak-free clamshell design – with interchangeable replacement parts
Precise temperature control and adjustable screw speeds – for optimum product quality
Easy cleaning and rapid switchover – with minimal downtime
High torque levels – across the range for seamless scalability
Screw elements – configured to your precise needs
Scalable solutions – from lab to big batch production
Technical
Specifications
PCX65
Screw diam: 65 mm
Speed: 1,200 rpm | 900 rpm
Capacity (max): 2,000 kg/h | 1,600 kg/h
PCX55
Screw diam: 55 mm
Speed: 1,200 rpm | 900 RPM
Capacity (max): 1,500 kg/h | 1200 kg/h
PCX45
Screw diam: 45 mm
Speed: 1,200 rpm | 900 rpm
Capacity (max): 900 kg/h | 600kg/hr
PCX33
Screw diam: 33 mm
Speed: 1,200 rpm
Capacity (max): 300 kg/h
PCX22
Screw diam: 22 mm
Speed: 1,200 rpm
Capacity (max): 80 kg/h
Volume throughputs will vary depending on use, material type, desired finish, and operator experience.
PCX65
Screw diam: 65 mm
Speed: 1,200 rpm | 900 rpm
Capacity (max): 2,000 kg/h | 1,600 kg/h
PCX55
Screw diam: 55 mm
Speed: 1,200 rpm | 900 RPM
Capacity (max): 1,500 kg/h | 1200 kg/h
PCX45
Screw diam: 45 mm
Speed: 1,200 rpm | 900 rpm
Capacity (max): 900 kg/h | 600kg/hr
PCX33
Screw diam: 33 mm
Speed: 1,200 rpm
Capacity (max): 300 kg/h
PCX22
Screw diam: 22 mm
Speed: 1,200 rpm
Capacity (max): 80 kg/h
Volume throughputs will vary depending on use, material type, desired finish, and operator experience.
Use this solution for
Processes supported
Extruding
Transform blended assortments of dry raw material ingredients into an evenly distributed and consistently dispersed homogeneous melts.
Portfolio showcase
Our ScatterPro portfolio

PCX extruders
Premium range of twin screw extruders offering industry-leading versatility and throughput.
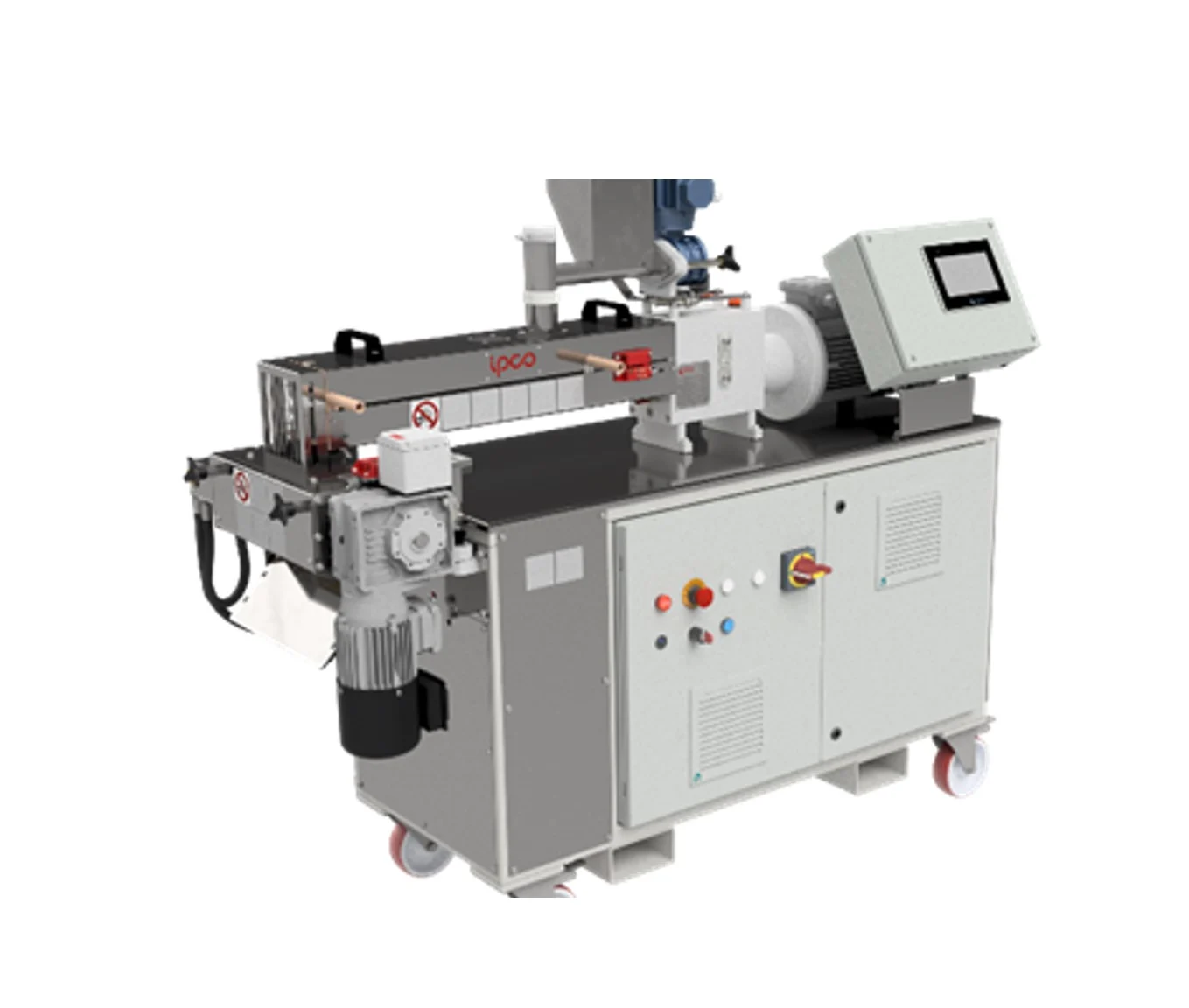
SCX extruders
Ideal for repeatable small-to-medium batch operations with low energy requirements.
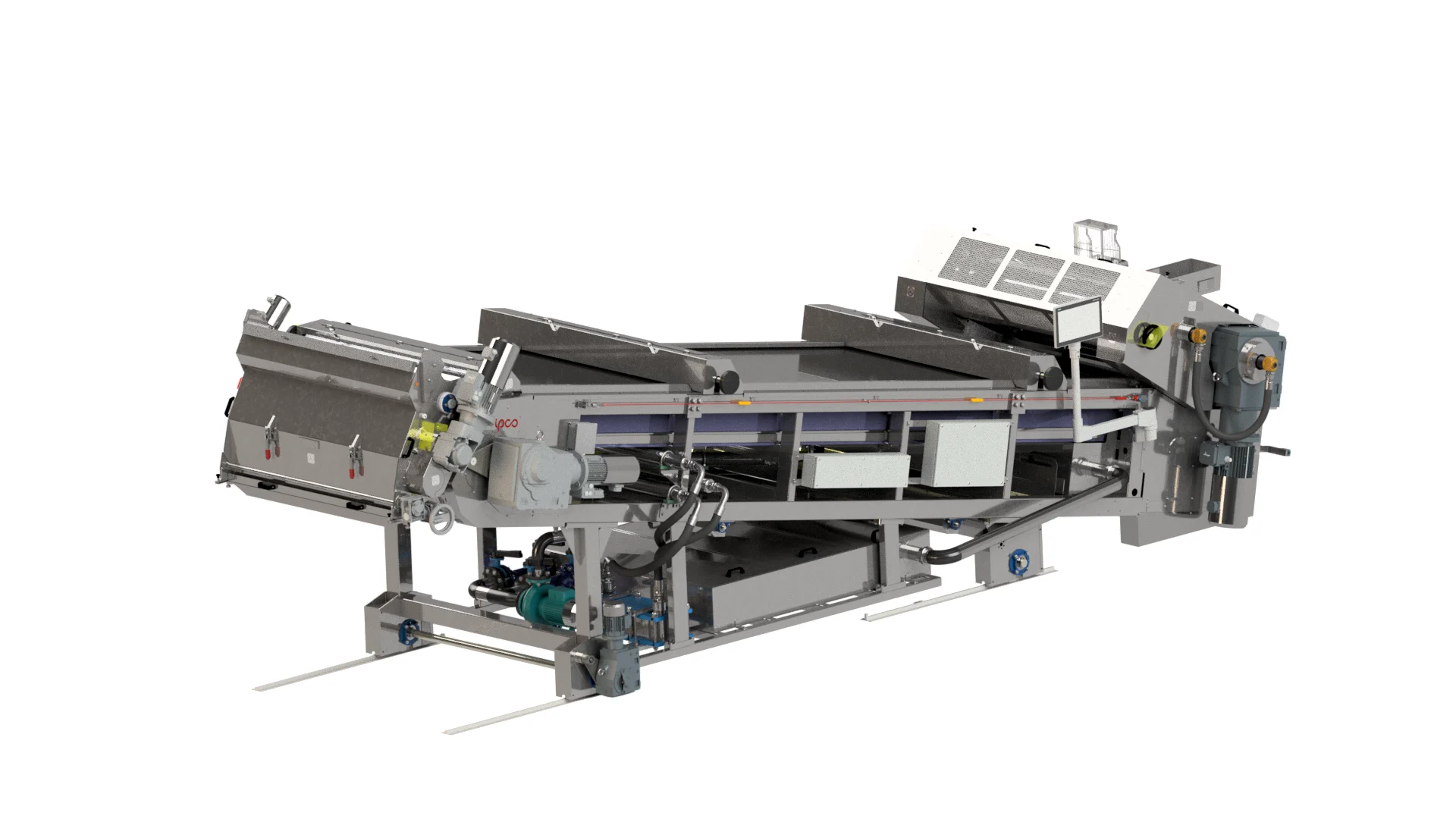
PCCB steel belt coolers
Low-maintenance stainless steel belt coolers for the solidification of a hot melt to a solid flake.