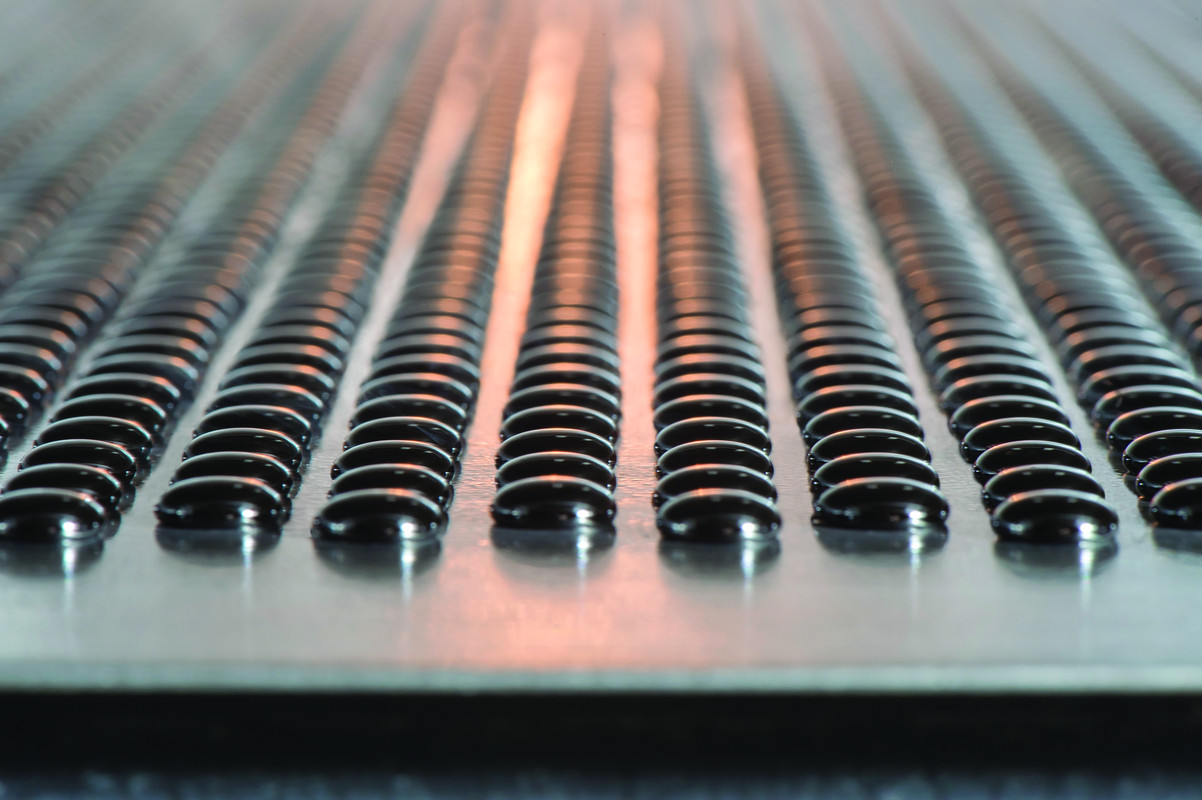
Refinery residual streams
As a refiner, technology licensor or business operating in the oil and gas industry, you face numerous challenges, from the need to comply with stringent emission mandates and clean fuel directives to variable prices and a constant focus on maximising production efficiency.
We can help you meet your business objectives through process solutions that combine market-leading performance, high levels of reliability for maximum uptime and more environmentally-friendly operation.
We offer a range of efficient solidification systems for the granulation, flaking and block forming of refinery residue products such as pitch and bitumen/asphalt. These are backed up by expertise gained through partnering with businesses like yours for more than 70 years. This means we can not only supply system solutions that satisfy your process needs but also offer you the depth of service to maximise your productivity and ROI.
Continuous solidification systems for value-added refined products
Factors such as the transition from fossil fuels to more sustainable technologies are likely to be leading you towards reconfiguring your existing assets and investing in Bottom of the Barrel (BOTB) technologies, with the goal of producing more value-added refined products for chemical production.
This means making greater use of processes such as residue & slurry phase hydrocracking, solvent de-asphalting, visbreaking and combinations of these.
The use of BOTB technologies enables you to significantly increase the conversion of crude oil, resulting in increased concentration of asphaltenes, petroleum carbon, catalyst residues and metals in the liquid pitch stream.
Solidification of CTP, SDA, PMB and more
Our systems enable you to convert molten residue streams into a solid form suitable for transportation, storage, dosing and reprocessing in downstream applications either inside or outside the refinery. We can help you convert typical residue streams such as:
- Coal tar pitch (CTP)
- Solvent de-asphalted (SDA) pitch
- Polymer modified bitumen (PMB)
- Oxidized bitumen / asphalt
- Coal slurry
- Pyrolysis residue
Versatile refinery residue process solutions
As the various BOTB processes differ, the resulting stream also varies from process to process and will place different demands on your solidification process in terms of:
- Melt temperature
- Feed temperature
- Softening point / penetration value
- Viscosity
- Solid impurities
- Residual solvent / DAO / UCO levels
As a major supplier of forming solutions for coal tar pitch (CTP), solvent de-asphalted (SDA) pitch and polymer modified bitumen (PMB), we at IPCO can design, manufacture and deliver a cost effective, reliable and more environmentally-friendly residue solidification process to suit your particular capacity and process requirements.
- Solidification directly from the melt.
- Highly uniform shape, stability and quality for easy storage and handling.
- Viscosities up to 15 000 mPas.
- Pastille diameters from 4 to 40 mm.
- More environmentally-friendly production.
- Ideal form for packaging, storage, blending and further processing.
- High capacity – steel belt cooling from above and below.
- Clean process – no exhaust air treatment required.
- Cooling water recirculated – no consumption, no contamination.
- Maximum productivity from limited floor space.
- Choice of feeding devices and discharge methods.
High speed bitumen asphalt block forming and packing system
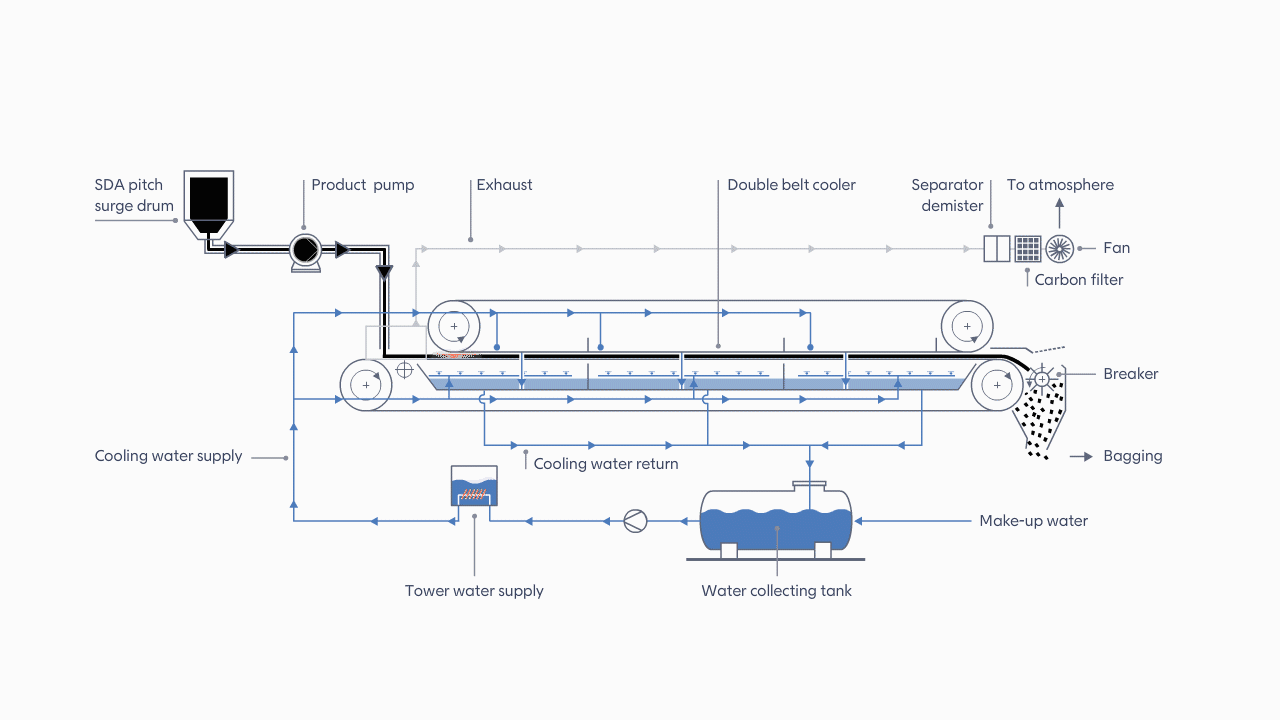
Depending on the end application, you may need to solidify bitumen in block form rather than pastilles. Our high speed block forming system enables you to produce regularly sized packs – directly from receipt of the molten bitumen – in little more than 15 minutes.
Your labor costs will be low too – automatic operation means you would need just two operators for a plant producing 10 000 tonnes of bitumen per year.
- Rapid, continuous oxidized bitumen packaging.
- Clean indirect cooling process – no water contamination.
- Low noise, easy removal of fumes.
- Standard 25 kg pack sizes: 710 x 345 x 100 mm.
- System includes shrink-wrapping.
High capacity
bitumen forming
2000
kg/hr
Download
- Case study – Bitumen solidification Case_Study_Etanchal
- White paper: Hydrocarbon Engineering White Paper 2021
- Rotoform pastillation
- Bitumen
- IPCO World